一、为什么从“遮阳板”切入谈乘用车内饰件制造?
遮阳板(Sun Visor)是乘用车驾驶舱中体积不大、动作频繁、与驾驶者交互最直接的功能性内饰件之一。它不仅承担遮挡阳光眩光、提升驾驶安全性的基础功能,还逐步集成了化妆镜、照明、气囊标签、传感器接口、文件夹卡槽等多种功能,是一个集结构、包覆、机构、电子与装饰于一体的“迷你内饰系统”。
正因为遮阳板涉及的工艺链条完整——从基体成型、五金件嵌件成型、泡沫填充、面料包覆、功能模块装配到外观与耐久检测——它可以作为一个极佳的切入点,延展到乘用车内饰件制造全流程的系统学习,包括材料、模具、工艺、质量控制、法规与轻量化趋势。
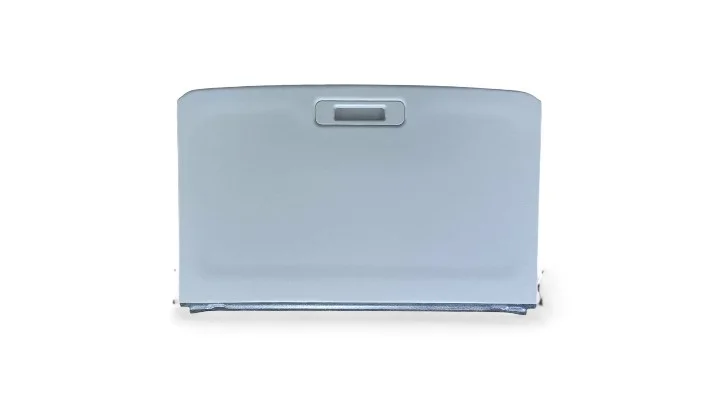
二、遮阳板的功能演进与产品类型
2.1 基础功能:遮挡直射与斜射阳光
- 主遮阳(前挡风玻璃上缘)
- 副遮阳(侧窗遮挡,可旋转)
2.2 集成功能升级
功能 | 描述 | 工艺影响 |
---|---|---|
化妆镜 | 翻盖式或无盖镜片集成 | 模具中需预留装配位或嵌件区 |
LED照明 | 镜框集成灯具或触控灯带 | 需走线槽、卡扣设计、热管理 |
票据/卡槽 | 可插票据、卡片 | 包覆层开口、装配公差控制 |
安全警示标签 | 气囊警示等 | 丝印、热转印或贴标工序 |
扩展滑轨 | 延展遮挡范围 | 机构复杂度提高,磨耗验证需加强 |
2.3 产品结构分类
- 硬芯 + 泡沫 + 织物包覆型(最常见)
- 注塑整体成型 + 表面软质漆/包覆型
- 复合材压制轻量化型(未来趋势,与车顶模块轻量化协同)
三、遮阳板材料系统解析
遮阳板由多个材料层级构成,典型结构示例:外表层(织物/针织布/PU皮)— 缓冲层(PU泡沫/PE发泡)— 基体骨架(PP/ABS/复合材)— 金属轴/转轴机构 — 附件(镜框、灯、电路)。
3.1 基体材料(结构强度核心)
材料 | 特点 | 应用备注 |
PP(带或不带玻纤) | 轻量、成本低、易注塑 | 对尺寸稳定性要求适中场景 |
ABS 或 PC/ABS | 尺寸精度好、表面质量佳 | 高端车型或功能复杂遮阳板 |
PA+GF | 高强度、耐热 | 主要用于转轴支座、小型嵌件 |
SMC/BMC复合材料 | 高强/耐热/可金属替代 | 轻量化趋势下的结构革新应用 |
3.2 内部缓冲/填充层
- 发泡PU(聚氨酯):柔软、填充性好、吸能。
- EPP/PE发泡片材:成型简便,可与包覆热合。
3.3 外饰表皮材料
表皮材料 | 外观/触感 | 工艺方式 | 等级定位 |
针织布/经编布 | 柔软、吸音 | 热压包覆、粘合 | 主流经济型 |
PVC皮革 | 成本可控、颜色多 | 热熔包覆、缝合 | 中端车型 |
TPU/PU人造革 | 手感佳、环保等级可提高 | 真空贴合、缝包 | 中高端 |
超纤/环保革 | 触感优、低VOC | 胶粘、包覆复合 | 高端豪华 |
四、遮阳板制造工艺总览
遮阳板制造通常包含多个串联或并联工艺段,取决于设计结构、材料体系与产量需求。以下为典型流程参考:
原材料准备 → 基体注塑/压制成型 → 五金轴/转轴嵌件 → 发泡填充或EPP装填 → 表皮包覆与热压整形 → 功能件装配(镜、灯、电线) → 外观检测 → 翻转耐久验证 → 包装出厂
4.1 基体成型(注塑或模压成型)
- 单片注塑 + 对合超声波焊接
- 左右壳对夹注塑 + 中空填充
- 模压成型(SMC/BMC骨架)适合耐热或刚度要求更高的车型
4.2 嵌件成型(Insert Molding)
将金属支杆、转轴连接件预放入模腔,注塑时包胶,实现结构与机构一体化,减少装配工序,提高配合精度。
4.3 发泡/填充工艺
- 低压发泡PU灌注:保证填充完整性与表面平整度
- 预成型泡沫片材热压复合:用于薄型、轻量化遮阳板
4.4 包覆与热压整形
- 热熔胶 + 真空吸附 + 热压刀边切口
- 皮革包缝 + 手工折边(小批量高端件)
- 高频热压成型(适用于PVC/PU薄皮)
4.5 功能件集成
- 化妆镜卡扣式装配或超声焊接
- LED灯引线嵌入槽,端子与车身线束对接接口
- 弹簧翻盖机构预装配
五、遮阳板模具设计要点(重点)
遮阳板模具是确保尺寸、外观、嵌件精度及包覆质量的基础环节。以下从结构、工艺、耐久与维护角度系统分析。
5.1 模具结构规划
- 型腔分型线:需兼顾包覆后不可见区域;避免在视觉区域留明显分型披锋。
- 嵌件定位:金属杆、转轴、镜框区域需添加精密定位销或磁吸定位块。
- 抽芯机构:遮阳板带滑动功能或凹陷区时需侧向抽芯;复杂零件可用液压斜顶。
- 壁厚均匀性:降低收缩不均与翘曲;建议主结构壁厚 2.5–3.5 mm(视材料定)。
5.2 浇注系统(浇口/流道)
模具类型 | 浇口形式 | 适用场景 |
边缘扇形浇口 | 薄壁、大覆盖面件 | 减少熔接痕 |
热流道点浇 | 多点充模 | 提升充模平衡 |
潜伏式浇口 | 美观要求高部件 | 减少浇口痕印 |
5.3 排气与缩痕控制
- 分型面排气槽深度典型 0.02–0.05 mm(视材料与模压压力)
- 镜框区域避免缩陷;必要时加强筋+工艺补缩点
5.4 模具钢材建议
模腔部位 | 推荐钢 | 特点 |
通用腔体 | P20 / 718 | 加工性好、成本适中 |
高光外观区 | 2738 / NAK80 | 可高抛光、纹理清晰 |
高磨损抽芯 | H13 / S136 | 硬度高、耐腐蚀 |
5.5 表面纹理与皮纹模拟
遮阳板包覆前后可能局部裸露基体,或模具用于生产面饰件替代件。可在型腔蚀纹(Grain)以模拟皮革纹理,增强视觉一致性;注意纹深与脱模角匹配。
5.6 可更换嵌块与平台化设计
- 多车系共用一副主模架,换嵌块实现不同镜框尺寸/延展滑轨结构。
- 标准化浇口、冷却系统,减少换模调试时间。
5.7 模流分析(Moldflow/Simpoe)导入点
- 熔接线位置预测(化妆镜开口周边)
- 翘曲仿真(长条形件、非对称壁厚)
- 包胶嵌件热传导影响
六、遮阳板与乘用车内饰件制造的工艺共性
从遮阳板延伸到更大范围的乘用车内饰件(如仪表板、门板、立柱饰板、顶棚、中央扶手、后备箱内衬),可总结出以下跨产品工艺共性:
工艺环节 | 遮阳板 | 仪表板 | 门板 | 顶棚 | 共性要点 |
基体成型 | 注塑/模压 | 发泡基体+表皮 | 注塑+包覆 | 玻纤基材压制 | 材料+模具精度决定尺寸 |
表皮包覆 | 布/皮革 | 发泡皮/包覆皮 | 皮革/织物 | 纤维毡+织物 | 包覆粘接性、热稳定性 |
嵌件集成 | 金属杆 | 气囊模块 | 扶手骨架 | 导线/传感 | 嵌件定位、热变形控制 |
表面纹理 | 可裸露 | 大面积可见 | 大面积可见 | 局部 | 模具纹理 & 包覆材料匹配 |
七、乘用车内饰件制造主流工艺技术合集
7.1 注塑成型(Injection Molding)
- 适用:立柱饰板、饰盖、小模块件、遮阳板骨架
- 关键参数:熔体温度、注射速度、保压时间、冷却回路
- 常见缺陷:缩水、翘曲、熔接痕、顶白
7.2 发泡注塑 / 轻量化发泡(MuCell、物理发泡)
用于减重、降低内应力、控制形变;适配大型仪表板骨架或厚壁内饰件。
7.3 热压成型(模压模塑)
- 材料:SMC、GMT、天然纤维增强片材
- 适合结构件 + 内饰二合一轻量化解决方案
7.4 真空成型 / 热成型(Thermoforming)
- 表皮片材预热后吸附于模具表面
- 常用于顶棚基材与软饰面覆盖
7.5 包覆(Wrapping / Lamination)
- 胶粘包覆、火焰复合、PUR热熔胶复合
- 自动化滚压线可实现高一致性装饰质量
7.6 超声波 / 热熔 / 激光焊接
内饰件对合、局部强化、卡扣替代螺钉装配的低成本方式。
八、内饰件模具设计的高级考虑因素
8.1 尺寸链与装配公差
遮阳板转轴到顶棚安装孔的装配偏差会直接影响旋转灵活性与异响;类似地,门板与仪表板、中央通道需要装配叠加公差控制。
8.2 热膨胀补偿
不同材料(塑料、泡沫、织物、金属)热膨胀系数差异大,模具需预补偿尺寸缩率;车内极端工况可在 -30°C ~ 85°C 之间循环。
8.3 表面等级分区
视觉A级面、触感B级面、隐藏C级面分区设计,优化模具成本。
8.4 快速换模与柔性制造
平台化模架 + 可换型腔模块,使一个生产单元可覆盖多车系、改款或不同配置(如遮阳板带灯/不带灯版本)。
九、质量控制与测试项目清单
遮阳板与乘用车内饰件必须通过多维度验证,以下列出常见测试项目(可扩展为企业检验SOP模板)。
9.1 外观与尺寸
- 三坐标(CMM)尺寸检测
- 表皮褶皱、气泡、刮痕检验
9.2 功能与耐久
- 遮阳板翻折寿命循环(≥ 10,000次,视OEM标准)
- 滑动/旋转扭矩保持力
- 卡扣装拆力
9.3 环境试验
试验 | 条件示例 | 判定 |
热循环 | -30°C ↔ 85°C 循环 | 无裂纹、变形可控 |
UV老化 | SAE J1885 或 OEM自定 | 褪色等级合格 |
盐雾 | ASTM B117 | 金属部件防腐 |
高湿 | 95%RH | 剥离、脱胶检查 |
9.4 安全与法规相关
- FMVSS 201(内饰件头部冲击性能,遮阳板区域相关)
- FMVSS 302(材料燃烧特性)
- ECE R21(内饰突起、半径要求)
- RoHS、REACH、VOC、气味等级
十、乘用车内饰件制造中的数字化与智能化
10.1 数字化研发
- CAD 3D主模型 + 参数化尺寸派生
- CAE仿真:热变形、刚度、碰撞、振动
- Moldflow 模流分析:浇口位置、充模平衡、翘曲预测
10.2 智能制造工厂场景
环节 | 智能化手段 | 效果 |
注塑车间 | 工艺参数闭环控制 | 降低批次间差异 |
包覆线体 | 视觉识别缺陷 | 实时剔除不良品 |
装配工站 | 扭矩感应电子拧紧 | 数据追溯 |
MES系统 | 批次追踪/工序溯源 | 质量可追溯 |
十一、轻量化与可持续发展趋势
汽车产业“双碳”与节能法规推动内饰件持续减重与环保化,遮阳板也不例外。
11.1 材料轻量化
- 发泡芯材替代实心塑料
- 生物基或循环再生PP/PE基体
- 天然纤维增强复合片(麻纤维、竹纤维)
11.2 工艺减材
- 局部增强 + 拓扑优化骨架
- 空腔化、蜂窝芯结构
11.3 环保与VOC
- 低气味胶粘剂
- 水性涂层与热压复合替代溶剂胶
- 内饰件 IMDS 数据上报与法规合规
十二、遮阳板项目开发流程(OEM/一级供应商协同示例)
以下为可复用的项目管理甘特式阶段划分(适配APQP框架)。
阶段 | 内容 | 交付物 | 风险点 |
RFQ技术评审 | 功能、尺寸、法规 | 技术澄清表 | 未识别法规差异 |
概念设计 | 包络、转轴机构 | CAD概念图 | 结构干涉 |
模流/DFM | 成型分析、模具拆件 | DFM报告 | 缩痕/翘曲风险 |
模具设计 | 分型、冷却、嵌件 | 模具2D/3D图 | 抽芯复杂度 |
T0试模 | 首件 | 外观尺寸数据 | 毛边、短射 |
T1/T2优化 | 工艺调试 | 改善报告 | 翘曲、披锋 |
PPAP/量产 | 批量验证 | PPAP文件包 | 过程能力不足 |
十三、遮阳板模具与乘用车内饰件的协同平台化策略
主机厂与大型内饰Tier-1正在推动部件平台化 + 外观差异化发展模式:
- 相同模架,不同面料颜色 & LOGO
- 相同结构,不同电气配置(带灯/不带灯、带传感器)
- 多区域法规版型共模(左驾/右驾、北美/EU标签差异)
这一策略降低模具投资与供应链复杂性,提升全球同步开发效率。
十四、遮阳板 & 内饰件成本控制要点
成本模块 | 影响因子 | 降本建议 |
模具 | 型腔数、钢材、纹理 | 共模设计、标准件化、模块化嵌块 |
材料 | 树脂、泡沫、表皮 | 替代材料、回收再利用、厚度优化 |
工艺 | 循环时间 | 热管理优化、自动化取件 |
装配 | 人工、返工率 | Poka-Yoke治具、自动化焊接/包覆 |
十五、FAQ:遮阳板与乘用车内饰件常见问题解答
Q1:遮阳板发泡不均导致外形鼓包怎么办?
A:检查模具闭合压力、灌注量、发泡剂温度;必要时增加排气孔或泡沫导流槽。
Q2:遮阳板旋转松旷异响?
A:转轴材料配对、公差堆栈、润滑脂选型、耐磨衬套改善。
Q3:包覆边缘翘起?
A:降低回弹材料张力、改进胶粘剂固化温度、增加折边夹具。
Q4:内饰件VOC超标?
A:更换低VOC辅料,延长烘烤挥发周期,材料供应商切换环保配方。